1. Deflate
Outgassing is the phenomenon of materials slowly evaporating in a vacuum, and is a major issue to be considered in terms of vacuum performance. In a vacuum system, on the surface of any solid material, there may be molecular layers formed by the accumulation of liquids and gases, and these molecular layers gradually evaporate as the pressure decreases. Inert gases and volatile solvents outgas relatively quickly, and water vapor and oil will adhere to the surface and evaporate after a few hours. Dust particles, porous materials, and other foreign objects increase the surface area of the system, which can cause more outgassing to occur.
Temperature and radiation will give some absorbed molecules enough energy to pull them off the surface. Raising the furnace temperature gradually releases molecules that would otherwise remain on the surface at lower temperatures. Therefore, as the furnace heats up, outgassing increases. Lowering the furnace temperature or maintaining a constant temperature can reduce this. Keeping it clean is key to reducing outgassing.
In addition, flushing with inert gas or nitrogen to exclude internal air can prevent the formation of a water vapor film when the system surface is exposed to air. This effect can also be achieved by heating the interior of the oven cavity after it has been opened. To minimize the number of furnace openings, especially in wet weather, can not reduce the occurrence of outgassing and improve the performance of the vacuum annealing furnace.
2. Evacuation rate
The evacuation speed is the time when the furnace chamber is at atmospheric pressure, the vacuum valve is opened, and the vacuum chamber reaches the specified pressure. It is a method of measuring system performance at any pressure (including pumping heavy mass gas). For reproducibility, the oven chamber should be cleaned, evacuated and vented, and each DVE vacuum pump should have been run for sufficient time to reach full pumping speed.
3. Ultimate vacuum
The ultimate vacuum is the vacuum state obtained by actually completing the deflation, at which time the flow of gas caused by the leakage and the ability of the vacuum suction system to exhaust at the specified pressure are balanced. To maintain correctness, vacuum measuring instruments must be sensitive enough and accurately calibrated. Raise the furnace to its maximum temperature to speed up the deflation of the system. After the furnace is heated under vacuum and cooled to room temperature, the true ultimate vacuum and leak rate can be measured. The ultimate vacuum of the DVE vacuum pump is called "extreme low pressure" and is a good way to achieve the isolation performance of the suction system.
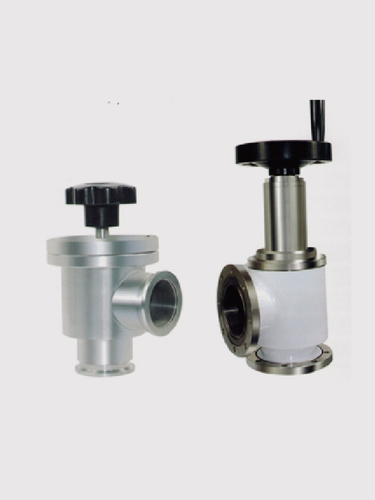
4. Leakage rate
The leak rate refers to the speed at which the pressure in the vacuum chamber rises when the vacuum is closed, and includes two aspects: the leak rate and the deflation rate. The leak rate is the pressure rise caused by the flow of gas through the actual leak point in the tank, which is constant; the deflation rate (including virtual leakage) is gradually approaching zero as the tank is emptied.
Void leakage is the volume entrained in the vacuum bulkhead that slowly leaks gas into the cabin. Leak rates are measured in micrometers of mercury (mmHg) per hour, usually measured for 1 hour, with a leak rate not exceeding 5mmHg per hour.
When measuring the pressure rise rate of the furnace cavity, empty the furnace cavity and start the circulating heating. After the deflation is completed, stop the heating until the pressure remains constant (ultimate vacuum), then close all the vacuum valves, and press the cycle stop button to isolate the furnace cavity.
This minimizes the effects of closing the valve while allowing the system to equilibrate. After one hour, measure the vacuum again and calculate the pressure rise per unit time. For example: if the measured initial pressure is 5mmHg, and after one hour it is 8mmHg, then the rising speed is 3mmHg per hour.